By adding a small amount of high-purity alumina silicate fiber binders, CCEWOOL® Ceramic Fiber back-lining Board is made through automation control and continuous production process, with a host of features such as precise size, good flatness, high strength, lightweight, excellentar thermal shock resistance and anti-stripping, which can be widely used for insulation in the linings around and at the bottom of kilns, as well as ceramic kilns fire position, craft glass mold and other positions.
Strict control of raw materials
Control impurity content, ensure low thermal shrinkage, and improve heat resistance
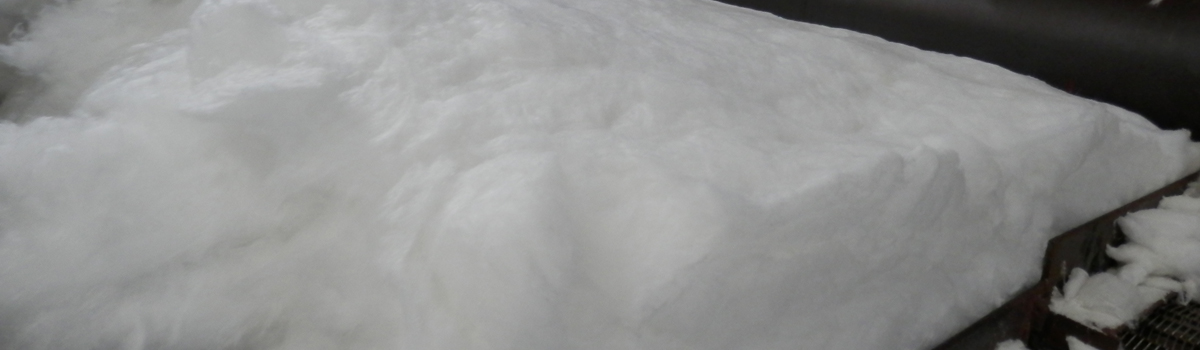
1. CCEWOOL ceramic fiber boards use high-purity ceramic fiber cotton as the raw material.
2. Controlling the content of impurities is an important step to ensure the heat resistance of ceramic fibers. High impurity content can cause the coarsening of crystal grains and the increase of linear shrinkage, which is the key reason for the deterioration of fiber performance and the reduction of its service life.
3. Through strict control at each step, we reduce the impurity content of the raw materials to less than 1%. The CCEWOOL ceramic fiber boards we produce are pure white, and the linear shrinkage rate is lower than 2% at the hot surface temperature of 1200°C. The quality is more stable, and the service life is longer.
4. With the imported high-speed centrifuge of which the speed reaches up to 11000r/min, the fiber formation rate is higher. The thickness of the produced CCEWOOL ceramic fiber is uniform and even, and the slag ball content is lower than 10%, leading to better flatness of the CCEWOOL ceramic fiber boards. The content of the slag ball is an important index that determines the thermal conductivity of the fiber, and the thermal conductivity of CCEWOOL ceramic fiberboard is only 0.112w/m.k at the hot surface temperature of 800°C.
Production process control
Reduce the content of slag balls, ensure low thermal conductivity, and improve thermal insulation performance
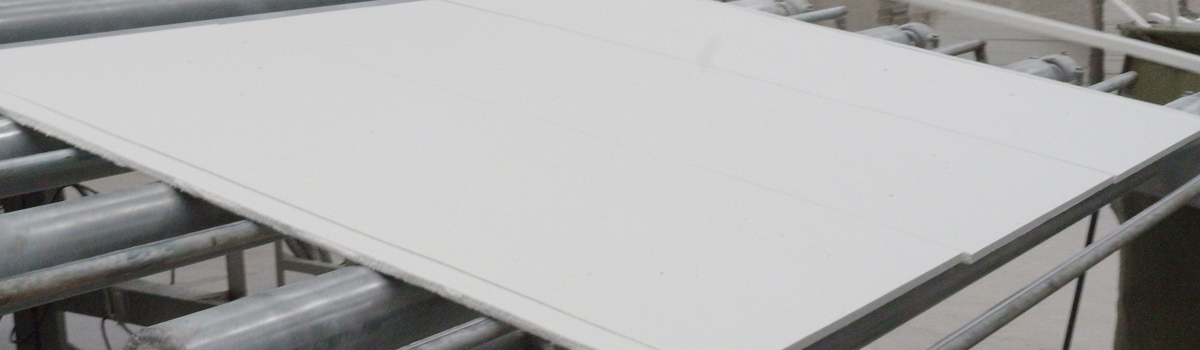
1. The fully automatic ceramic fiber production line of super large boards can produce large-size ceramic fiber boards with a specification of 1.2x2.4m.
2. The CCEWOOL Ceramic Fiber Back-lining Board production line has a fully automatic drying system, which can make drying quicker and more thorough. The deep drying is even and can be completed in 2 hours. The products have good dryness and quality with compressive and flexural strengths over 0.5MPa.
3. The products produced by the fully automatic ceramic fiber board production lines are more stable than the ceramic fiber boards produced by the traditional vacuum forming process. They have good flatness and accurate sizes with the error +0.5mm.
4. CCEWOOL Ceramic Fiber Back-lining Board can be cut and processed at will, and the construction is very convenient. They can be made into both organic ceramic fiber boards and inorganic ceramic fiber boards.
Quality control
Ensure bulk density and improve thermal insulation performance
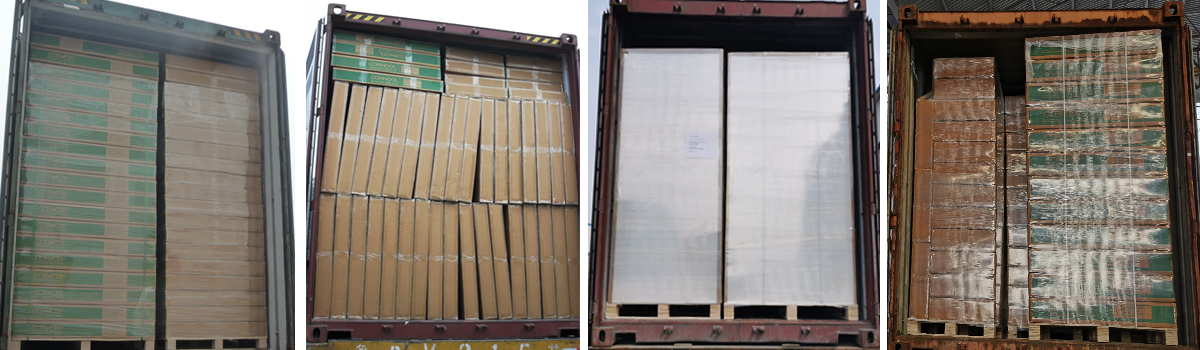
1. Each shipment has a dedicated quality inspector, and a test report is provided prior to the departure of products from the factory to ensure the export quality of each shipment of CCEWOOL.
2. A third-party inspection (such as SGS, BV, etc.) is accepted.
3. Production is strictly in accordance with ISO9000 quality management system certification.
4. Products are weighed before packaging to ensure that the actual weight of a single roll is greater than the theoretical weight.
5. The outer packaging of each carton is made of five layers of kraft paper, and the inner packaging is a plastic bag, suitable for long-distance transportation.
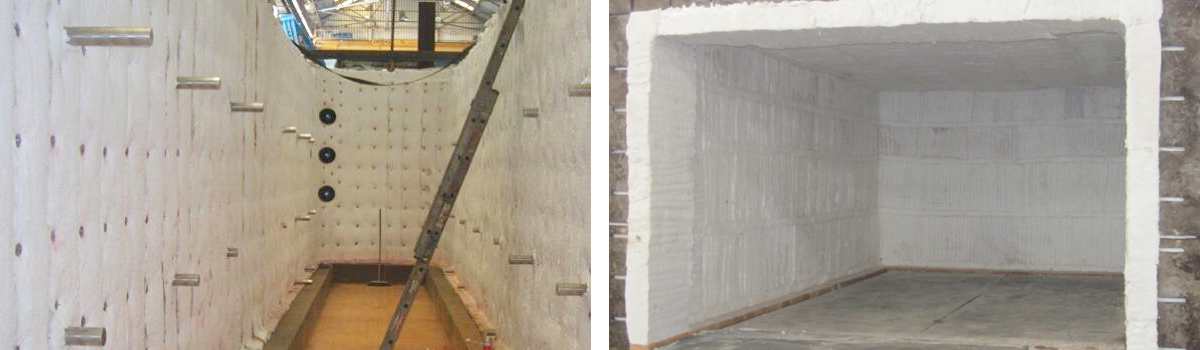
Characteristic of Ceramic Fiber back-lining Board:
Low heat capacity, low thermal conductivity;
High compressive strength;
Non-brittle material, good elasticity;
Accurate sizes and good flatness;
Easily molded or cut, easy to install;
Continuous production, even fiber distribution and stable performance;
Excellent thermal stability and thermal shock resistance.
Application of Ceramic Fiber back-lining Board:
Cement and construction materials: furnace back thermal insulation lining;
Ceramics industry: lightweight kiln car structure and the furnace hot face lining, separation and fire position for all kiln temperature zones;
Petrochemical industry: as high-temperature furnace hot surface lining material;
Glass industry: As furnace hearth back insulation lining, burner blocks;
Hot surface refractories, heavy refractory back linings, expansion joints;
Firebrick back lining for tundish, slot cover and aluminum plant electrolytic reduction cell;
All heat treatment furnace lining, expansion joints, backing insulation, thermal insulation and mold insulation, steel mill ladle, tundish, ladle and refined ladle back linings.
-
Guatemalan Customer
Refractory Insulation Blanket - CCEWOOL®
Cooperation years: 7 years
Product size: 25×610×7620mm/ 38×610×5080mm/ 50×610×3810mm25-04-09 -
Singapore Customer
Refractory Ceramic Fiber Blanket - CCEWOOL®
Cooperation years: 3 years
Product size: 10x1100x15000mm25-04-02 -
Guatemala Customers
High Temp Ceramic Fiber Block - CCEWOOL®
Cooperation years: 7 years
Product size: 250x300x300mm25-03-26 -
Spanish Customer
Polycrystalline Fiber Modules - CCEWOOL®
Cooperation years: 7 years
Product size: 25x940x7320mm/ 25x280x7320mm25-03-19 -
Guatemala Customer
Ceramic Insulating Blanket - CCEWOOL®
Cooperation years: 7 years
Product size: 25x610x7320mm/ 38x610x5080mm/ 50x610x3810mm25-03-12 -
Portuguese customer
Refractory Ceramic Fibre Blanket - CCEWOOL®
Cooperation years: 3 years
Product size: 25x610x7320mm/50x610x3660mm25-03-05 -
Serbia customer
Refractory Ceramic Fiber Block - CCEWOOL®
Cooperation years: 6 years
Product size:200x300x300mm25-02-26 -
Italian customer
Refractory Fiber Modules - CCEWOOL®
Cooperation years: 5 years
Product size:300x300x300mm/300x300x350mm25-02-19